AOTEK’s engineers have an accumulated experience of many man-years in control loop design and tuning. A highly skilled team supports OEMs to enhance their machines dynamical behaviour from optimal tuning of the FAGOR drives to sensible suggestions on mechatronics design.
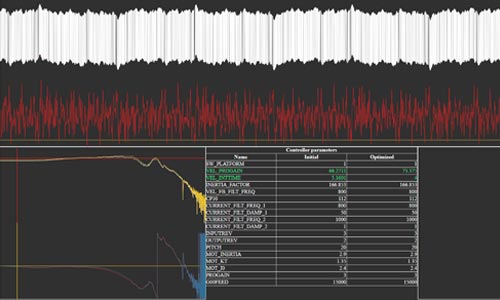
Model-based design support
AOTEK’s engineers routinely use model-based technologies to build and test control loops, like active damping, non-linear compensations… This is an excellent background to support OEMs to build model of the machine kinematics chains and integrate them in the CNC simulator, providing a Digital Twin of the machine tool.
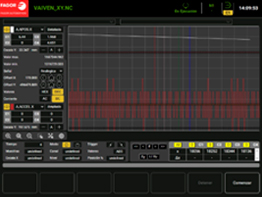
Machine dynamics analysis and identification (linear and non-linear)
Key for the correct tuning of control loops and diagnosis of kinematic chains is an accurate model of its dynamic characteristics. AOTEK’s tools and skilled team can afford this task for complex systems including non-linear effects like backlash and friction.
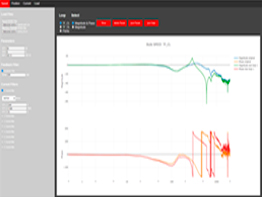
Automatic tuning of control parameters and control loop optimization
AOTEK’s accumulated experience has been integrated in a tuning application where the different steps, from transfer function identification to optimal setting of relevant parameters are carried out under OEM’s engineer control. This is the best solution for many standard machines where robust, conservative tuning is required. For more demanding machines, AOTEK’s support is available to find the highest stable bandwidths.
Artificial intelligence, machine learning
AOTEK has lead projects on the use of Artificial Intelligence techniques in several tasks related with optimal parameter settings and kinematics chain diagnosis for condition based maintenance. Knowledge of these techniques is allowing AOTEK to tackle with complex problems with non-linear behaviour and many involved variables. This is currently an evolving activity that is influencing other stablished technologies.
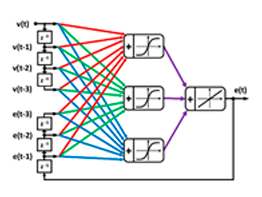
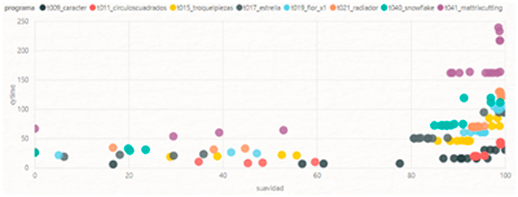